It is the year 1991. Imagine a bar, filled with cigarette smoke, a few long-haired men in leather jackets are bent over pool tables. Arnold Schwarzenegger enters the stage. In his birthday suit. “I want your clothes, your boots and your motorbike your power drill.”
What has been a small step for Arnold, was a large step for film history. Until today, images such as of the T-900 shape our idea of artificial intelligence (AI). AI reminds some of Terminator, Matrix or Blade Runner, while others think of chess playing computers and self-flying taxis. That this technology is not a distant future, but could very soon be part of everyday life, has now arrived in most minds. But no one thinks of tunnel and civil engineering – a mistake if you are listening to Helmut Wannenmacher.
Within the context of his professional activities and his part-time studies Helmut works on the implementation of AI in tunnel and civil engineering. His goal is to be able to react faster to unforeseen changes during construction.
*****
Let’s start at the beginning. As everybody knows, during grouting large amounts of data accrue (our specialty). This data is collected, recorded in protocols and submitted to construction supervisor, client or planner – the interpretation of these data can take a few days, which is problematic as the recorded data is the only parameter that tells you whether an injection has reached the injection goal. “You do your job, put a packer in somewhere and push the suspension in, but you cannot see the overall result”, says Helmut. “The only possibility you have got to make this result visible, is your injection report – the evaluation of your parameter; the evidence that you have done your work according to the specifications.”
The evaluation of existing data sets with a little basic geo-mechanical understanding (Helmut’s specialty) should ultimately answer the question, whether the injection target was reached – which would be: to improve or seal the subsoil through a rock injection or something similar, and to sustainably change the structure of the material.
To do this, the planning engineer creates a kind of conceptual model which defines how much material must be brought into the subsoil at which maximum pressure in order to achieve a desired result without tearing up the subsoil.
On the basis of this model it can be compared if the right amount of material was introduced, or whether the maximum pressure was reached or not. What is NOT answered by the model is the question if the injection goal was reached in reality.
That is due to of the unpredictability of the flow path of the injection. Therefore, it is not possible to say with an absolute certainty whether the injection was successful or not, only because high suspension or a high pressure was introduced. New approaches for the understanding of the injection are needed; approaches which can ultimately handle such uncertainties and which reach the injection goal regardless of any influence factors, means Helmut.
Gone astray?
The conceptual model defines how much volume of injection material needs to be introduced under which pressure. A deviation of this straight path towards the goal always results in changes that can affect the injection. But if it takes a few days until the data sheets are created, submitted and interpreted, mistakes and deviations are only noticed when it is already too late. “That´s the crux of this matter”, says Wannenmacher: “How much time do I have to react to a negative deviation? In order to react adequately, you need computer support because the injection system is too complex to constantly monitor it during the execution.”
All data patterns need to be classified according to their geo-mechanical behaviour. This is where it starts to get complicated. Together with Harald Krenn, division manager at Trevi Geotechnik Vienna, Harald Wannenmacher has come up with a system to quantify the deviations not only according to pressure and flow rate, but according to the behaviour of both parameters on the basis of previous values.
Curves in all the right places
After all, injection graphs are curves. Curves can be quantified according to their slope. Is the slope of a curve zero, the system has not changed. But if the slope of curve is larger than zero, a parameter of the system has changed (see figure 1). “This slope that can be observed is the first deviation. You can combine the first deviation of pressure and first deviation of the flow rate in a graph, convert it to a pattern and classify it.”

The identification of these patterns is the topic of a joint R&D project. But instead of importing the patterns into the AI straight away, the engineers included an intermediate step and handled the pattern recognition manually. “It is important to me to combine geo-mechanical expertise with data evaluation”, says Wannenmacher.
The most important question which arises with these consideration is the question of time: Do I have enough time to react to a recognised pattern adequate? “The question is, if it is possible to influence a pattern positively by the use of the latest technologies. We assume that it is possible. We just have to be able to measure and react fast enough”, Wannenmacher is convinced – because if it were otherwise, the whole consideration would be meaningless.
Learning from experience
For this aspect of reaction time, artificial intelligence comes into play. To recognise a pattern and its meaning, the injection parameters have to be checked and the result needs to be assigned to an already known pattern.
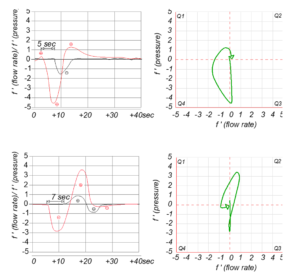
AI is able to recognise these patterns. In order for a computer to find and interpret similar patterns, more mathematical specifications need to be imported to the AI for it to study and learn. Wannenmacher uses eguana SCALES for this, where he can easily and quickly search for simultaneous patterns in the data base – of course not by himself. “For this I need the AI of eguana SCALES: to recognise many patterns. If they can be recognised, the computer can tell how we could have reacted to the deviation.” The algorithm can learn from this experience. “I think AI can be a great support to the pump operator to execute several injections simultaneously without any errors. The computer must take over the ongoing control, since the reaction times require an immediate just-in-time reaction. This is a new and essential step that we are planning together.”
On the side, Harald collaborates with eguana on exciting, new projects – we hope to welcome him again soon with a new progress report here with us. Until then we say: Hasta la vista, baby – We´ll be back!” (to loosely quote Terminator)
*****
We want to thank Helmut Wannenmacher for his expertise, time and patience (artificial intelligence is not necessarily my speciality), and are looking forward to future collaborations!
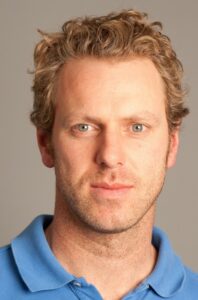
About the guest author Helmut Wannenmacher:
Churchill once said: There is something about the outside of a horse that is good for the inside of a man. Well, for Helmut Wannenmacher that is certainly true – as long as the horse is made of iron. When he is not working for Implenia Austria or excels in his PHD studies at the RWTH Aachen, he can usually be found whereever you can drag a bike up a mountain and race down.
Born and raised in Tyrol, Helmut has successfully completed projects all over the world. They have taken him from North to South America, to Africa, to the Middle East and Asia. Currently he works at the Semmering base tunnel and is responsible for the execution of the biggest injection procedure in Austria at the Baulos 1.1. The “strong belief that computer will make work easier and that we can gain more free time” is what drives the busy multitasker.
If that was not enough information, just hop on a bike and look for the next mountain. Or just click here.
*****
“I talked to the pump computer.”
“And?”
“It hates me.”
(loosely based on The Hitchhiker’s Guide to the Galaxy)
*****
Stephen Hawking: “Artificial intelligence may replace humans altogether.”