“Wherever he saw a hole he always wanted to know the depth of it. To him this was important. ”
The path of Thorsten Kratz might not lead all the way to the center of the earth, but nevertheless into unknown depths. In the best manner of science-fiction-prophet Jules Verne, the civil engineer and project manager at Thyssen Schachtbau GmbH, sets out to explore the subsoil – with exploratory drilling.
The aim of these drills is to collect drill cores or cuttings to gain knowledge about the location, thickness and mineral content. On the basis of those informations, decisions about the dismantling and the dismantling process can then be made. In tunneling construction, exploratory drilling is also about obtaining information about tectonic fault zones, mountain sections carrying mountain water and the like.
At shallow depths of up to 100 meters, drilling core extraction with single core tubes and double core tubes is still relatively easy. In this process, the drill core is recovered by removing the drill string. At depths of up to 2,000 meters, the so-called cable core process is used, in which the drill rod plays a protective role while the inner core tube is recovered using a cable winch. The drill cores that are recovered are between 26 and 102 millimeters thick.
We asked Thorsten Kratz how such exploration wells work, talked about exciting projects and obstacles and took a look into the future.
Curtain up for the contemporary Professor Lidenbrock!
*****
eguana: What differentiates you and your drilling from the competition?
Thorsten Kratz: The complexity of a drill results from its destination and the given framework conditions.
Challenging goals and framework conditions are, for example:
*) Drilling depth> 100 m –> Powerful drilling rigs
*) Water or gas carrying –> Complex borehole closure device (preventer)
*) instable Borehole –> Casing or cementation program
*) drilling accuracy –> deflected or controlled drilling
*) underground drilling site –> little space, limited infrastructure, explosion protection
*) drilling direction horizontal –> no supporting effect of the flush
*) Drilling fluid –> Mud fluid (water / air) + additives
As soon as one or more of the points mentioned above apply within the project requirement, special drilling equipment and personnel are required in order to be able to carry out the drilling at all. Thyssen Schachtbau GmbH carries out a large number of these highly specialized drilling projects. To name a few:
*) Horizontal, deflected core drilling in potash and rock salt mining under preventer protection (gas) with drilling depths of up to 2,500 m
*) Oriented core drilling in rock salt with air flushing up to 450 m
*) Horizontal exploratory drilling under prevention protection (water up to 100 bar) in tunnel construction with drilling depths of up to 300 m.
*) Erosion-resistant overburden boreholes up to 150 m
*) Vertical, controlled core drilling with drilling depths of up to 1,200 m for the exploration of deposits or locations of future mine shafts
*) Vertical and horizontal controlled freeze drilling down to depths of approx. 800 m for carrying out ground freezing
*) Inclined, controlled large hole bores with a diameter of> 300 mm and drilling depths of up to 800 m as pilot bores for raise bores.


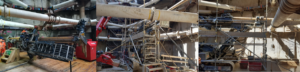
Every time I want to screw something to the wall at home, I am sure to choose a spot where drilling is impossible. To make things really frustrating, this usually happens at the second hole, making my wall look like a slice of emmental cheese. How is it with large-scale drilling? Does it also happen that you have already made it halfway and then come across an impenetrable layer of rock? Or do you get through everything?
It would be nice, but certainly a lie, to say that we can drill through any rock or mountain. Every drilling process is subject to device-related or process-related application limits. In difficult conditions, the basis of a successful drilling is good planning and work preparation as well as experienced drilling staff.
However, the past shows that even then a drilling can fail.
For example, we were unable to drill through a large fault zone with the contractually required core drilling process, since, due to a lack of borehole stability, no irrigation circulation came about and the drill string subsequently got stuck. In this special case, changing the drilling method to an overlay drilling, in which the casing is carried directly with the drilling process, was the solution.
If we were in Hollywood, such an exploratory drilling would be sure to trigger an exciting catastrophe: starting with a simple gas leak and releasing primeval killer bacteria to reversing the earth’s rotation (presumably because the drill touches an acupuncture point in the earth’s crust unfavorably ). What is the reality like – are there reasonable scenarios to be “feared”?
The risk of a borehole damage is particularly given when drilling against high water or gas pressure. The term Borehole damage means that the medium flowing into the borehole flows out of the borehole in an uncontrolled manner. To prevent such situations, we work with so-called “borehole closure devices” or preventers, as they are basically known from the oil industry. Depending on the application, the modular structure of such preventers enables drilling with water ingress of up to 200 bar pressure. In the event of an incident, the drill string can be cut in seconds with a so-called shear preventer, thus closing the borehole completely. This type of preventer cannot be compared with the annular space preventer and spade gate valves used in the construction industry.
As with water inflows, drilling in gas-bearing rock requires technical adaptations: On the one hand, a preventer is usually also used, which can, if necessary, lock the gas inflow in the borehole. It is also necessary to carry out electrical and electronic system parts (drive, sensors, etc.) with explosion protection.
Have you ever come across a completely unexpected drill core? Do you sometimes find really exciting things? A small diamond deposit?
We have already carried out exploratory drilling for a mining company in an open-cast diamond mine in Botswana, but unfortunately we were not able to recover any high-carat diamonds from the kimberlite vent with the drill cores that were extracted.
Basically, it is in the nature of things that unpredicted geologies are encountered during exploratory drilling. It’s rarely spectacular, but often technically challenging, which is what makes the work so exciting.
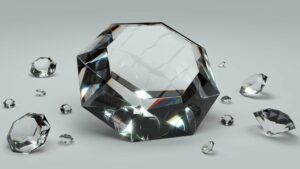
Does the hole stay open at the end? Is it very tempting to drop a stone and listen to when it hits?
If further use of the borehole is planned, piping is usually installed after the borehole has been completed. If this is not the case, boreholes are often filled with cement and thus sealed.
What kind of projects do you have going on in this regard? Exciting completed projects or interesting findings?
In the area of exploration wells, my focus is on our project on the Semmering Base Tunnel, construction lot 1.1. The difficult geology is quite a challenge, and not only from a drilling point of view. It repeatedly calls for creative solutions.
Another exciting project, which unfortunately will probably soon be interrupted indefinitely, is the Brenner Base Tunnel. Here, exploratory boreholes are sunk out of the exploratory tunnel in the direction of advance. Water pressures of over 100 bar are forecast, which require the use of special prevention technology.
In Serbia we recently drilled raise bores into a limestone quarry. The shafts with a diameter of 3.50 m and a depth of approx. 120 m serve as rubble shafts for the quarry and primarily reduce wheel-based transport, which, above a certain distance, brings economic and emission disadvantages with it. In addition to technical challenges (e.g. in relation to the lack of stability of the mountains) the issues relating to logistics, mining permits and material supply in a non-EU country with a remote project location could be mastered.
A look into the future – what will things look in five years?
As far as drilling technology is concerned, no technically significant leaps in development are to be expected in the coming years. Rather, the focus will be on using the drilling data that are already frequently recorded and contractually required. The basis lies in an efficient as possible digital drilling data management, which houses some optimization potential. The digitization of the drilling data reduces the documentation effort and increases the quality of the data at the same time. The transparency and usability of the data enable the identification of problem areas, the analysis of performance and consumption quantities and thus form the basis for calculation, controlling and construction site management in general. In further steps it is possible to define process assignments based on the drilling data, visualize processes accordingly and automatically generate measurement and accounting sheets for the customer.
*****

“Anything one man can imagine, other men can make real,” Jules Verne once wrote. We have not yet made it all the way to the centre of the earth, but coming as far as Thorsten has, was nothing more but a distant dream during Vernes lifetime. At the end of the 1970s, the to date deepest borhole in the world penetrated to depths of over 12 kilometers, and yet only scratched the earth’s crust. Around 6,000 kilometers are missing to the actual center of the earth – but who knows what the future will bring. Perhaps the science fiction prophet, who dreamed of submarines as early as the mid-19th century, will be right with a trip to the center of the earth.
*****
About Thorsten Kratz:
Like Professor Lidenbrock, Thorsten Kratz comes from Germany. The mining engineering graduate worked as a research assistant at the Institute for Mining Studies I at RWTH Aachen University in the research field of conventional shaft sinking during his doctorate. After completing his doctorate, he moved on to work for Thyssen Schachtbau GmbH, where he is now working as a project manager in the Alpine and Balkan region for infrastructure and mining projects with a focus on tunnel and shaft construction, raise-boring, exploration drilling and injection technology. His main project is the Semmering Base Tunnel, construction lot 1.1, which he has been involved in since the beginning as a member of the technical management.
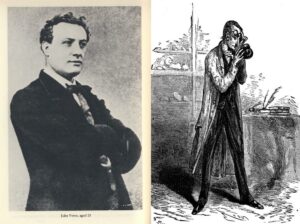
Thorsten Kratz – more Jules Verne or Otto Lidenbrock? (Credit: Wikimedia Commons)